The Role of Digital Twins in Revolutionizing Manufacturing Processes
4 Aralık 2024
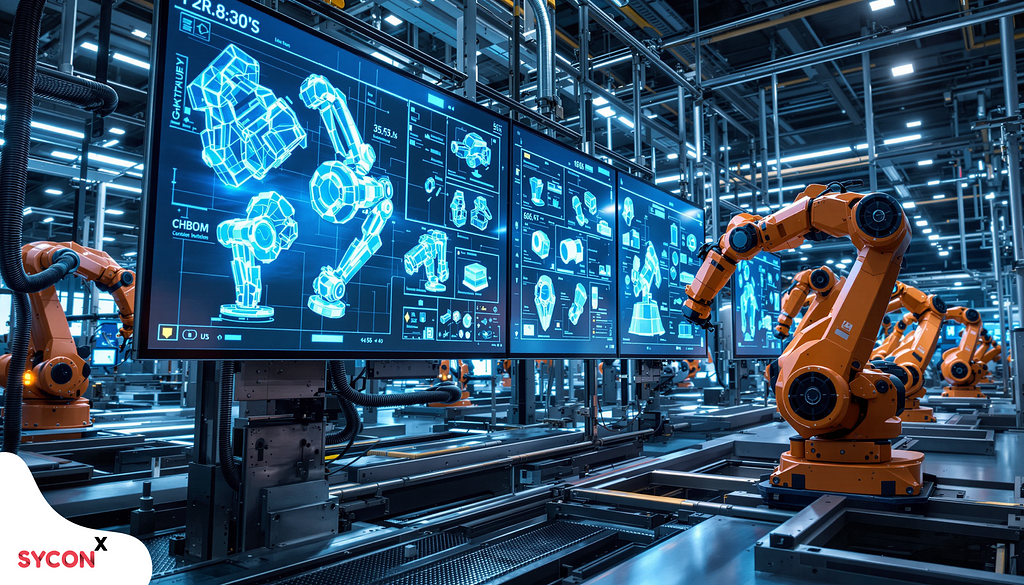
In today’s rapidly evolving technological landscape, the concept of digital twins has emerged as a transformative force in manufacturing. By creating a virtual replica of physical systems, processes, or products, digital twins enable unprecedented levels of insight, efficiency, and innovation. From predictive maintenance to streamlined production workflows, the application of digital twins is reshaping traditional manufacturing practices and setting the stage for Industry 4.0.
What is a Digital Twin?
A digital twin is a dynamic virtual model of a physical entity, continuously updated with real-time data from its physical counterpart. This virtual representation mirrors the behavior, conditions, and performance of the physical object, allowing for simulation, analysis, and optimization without interfering with the actual system.
The essence of digital twins lies in their ability to integrate data from sensors, IoT devices, and advanced analytics. This integration provides manufacturers with a comprehensive understanding of their operations, enabling informed decision-making and innovation.
The Core Benefits of Digital Twins in Manufacturing
1. Enhanced Predictive Maintenance
One of the most impactful applications of digital twins in manufacturing is predictive maintenance. By monitoring the real-time performance and condition of equipment, digital twins can forecast potential failures before they occur. For instance:
• Sensors in a production line feed data to the digital twin.
• Algorithms analyze this data, identifying patterns that indicate wear and tear.
• Alerts are sent to technicians to address issues proactively.
This approach reduces unplanned downtime, extends the lifespan of machinery, and minimizes operational costs.
2. Improved Product Design
Digital twins facilitate the design and testing of products in a virtual environment. Engineers can:
• Simulate different scenarios to optimize designs.
• Test materials, stress levels, and environmental conditions.
• Incorporate customer feedback seamlessly into the design process.
By identifying flaws early in the development stage, manufacturers can significantly reduce the cost and time associated with prototyping.
3. Streamlined Production Processes
With real-time visibility into every aspect of the manufacturing process, digital twins help optimize production lines. For example:
• Bottlenecks can be identified and resolved.
• Energy consumption and resource utilization can be analyzed and reduced.
• Workflow simulations can help rearrange production layouts for greater efficiency.
4. Enhanced Quality Control
By monitoring production in real time, digital twins ensure that products meet stringent quality standards. Data from the physical product is continuously compared to the ideal specifications stored in the digital twin. Any deviations trigger immediate corrective actions, ensuring consistent quality.
Key Technologies Enabling Digital Twins
Digital twins rely on a combination of advanced technologies to function effectively:
• Internet of Things (IoT): IoT devices collect and transmit real-time data from the physical world to the digital twin.
• Artificial Intelligence (AI) and Machine Learning: AI algorithms analyze data, identify patterns, and provide actionable insights.
• Cloud Computing: Cloud platforms offer the storage and computational power required to handle large volumes of data.
• Augmented Reality (AR) and Virtual Reality (VR): AR and VR interfaces enable immersive visualization and interaction with digital twins.
These technologies work in tandem to create an ecosystem where digital twins can thrive.
Practical Applications in Manufacturing
1. Automotive Industry
Automotive manufacturers use digital twins to enhance vehicle design, assembly lines, and maintenance. For example:
• Tesla employs digital twins to monitor and improve the performance of its electric vehicles.
• Virtual replicas of assembly lines help optimize the production process, reducing waste and improving efficiency.
2. Aerospace and Defense
The aerospace sector leverages digital twins to ensure the reliability of complex systems such as jet engines. Real-time monitoring of engine components allows manufacturers like Rolls-Royce to predict failures and schedule maintenance efficiently.
3. Electronics Manufacturing
In electronics manufacturing, digital twins help optimize high-precision production processes. They ensure that microchips and circuit boards meet exacting standards, reducing the likelihood of defects.
4. Consumer Goods
Digital twins enable consumer goods manufacturers to experiment with packaging designs, simulate supply chain logistics, and ensure product consistency across global markets.
Challenges in Implementing Digital Twins
Despite their immense potential, digital twins face certain challenges in adoption:
• Data Integration: Manufacturers must integrate data from various sources, which can be complex and time-consuming.
• High Initial Investment: Developing and deploying digital twins requires significant upfront costs.
• Cybersecurity Risks: Real-time data exchange between physical and digital systems increases the risk of cyberattacks.
• Skill Gap: Manufacturers need skilled professionals to develop, manage, and utilize digital twin systems effectively.
Addressing these challenges requires strategic planning, investment in workforce training, and robust cybersecurity measures.
The Future of Digital Twins in Manufacturing
The role of digital twins is set to expand as technology evolves. Key trends shaping the future include:
1. Integration with AI and Edge Computing
Combining digital twins with AI-driven analytics and edge computing will enhance real-time decision-making and reduce latency.
2. Sustainability Initiatives
Digital twins will play a pivotal role in achieving sustainable manufacturing by optimizing energy consumption and minimizing waste.
3. Collaboration Across the Supply Chain
By integrating digital twins across supply chains, manufacturers can enhance collaboration, improve transparency, and respond swiftly to disruptions.
4. Advancements in Simulation Technologies
Improved simulation capabilities will allow manufacturers to model even more complex scenarios, further enhancing productivity and innovation.
Digital twins represent a paradigm shift in manufacturing, offering unprecedented opportunities for efficiency, innovation, and sustainability. By enabling real-time insights, predictive capabilities, and seamless integration of physical and digital realms, they are transforming how manufacturers design, produce, and maintain products.
As manufacturers overcome adoption challenges and embrace this technology, digital twins will undoubtedly become a cornerstone of the smart factories of the future, driving the next wave of industrial revolution.
The Role of Digital Twins in Revolutionizing Manufacturing Processes was originally published in SyconX on Medium, where people are continuing the conversation by highlighting and responding to this story.